One minute Peri & Sons Farms is celebrating its ability to grow 150 acres of different lettuces in Nevada’s Mason Valley. Next thing you know, the company — reported to be the largest white onion grower in the United States — suddenly finds itself the focus of news reports with headlines, such as Field Gas Irritates 125 Farm Workers and Ag Chemical Incident Sends Nearly 120 to Hospital and 125 Nevada Farm Workers Sickened By Chemical and Chemical Fumes Overcome 130 — Yerington Farm Workers Afflicted.
One of the lessons is how deceptive headlines can be. The 120 people who were “sent to the hospital” were actually sent to a triage center set up in parking lot of a medical center. If the triage center happened to be set up in the parking lot of a high-end spa, we suppose the headline would have read “Ag Chemical Incident Sends Nearly 120 to a Luxury Spa.”
Wanting to both understand the substance of what happened and to draw lessons from the experience for the broader industry, we asked Pundit Investigator and Special Projects Editor Mira Slott to learn more:
![]() |
Pam Peri Executive Vice President Peri & Sons Farms |
![]() |
Tim Cummings Director of Marketing and Public Relations Peri & Sons Farms |
![]() |
Russell Wedlake General Manager and Safety and Training Officer Silverado Ranch Supply |
![]() |
Ed Foster Regional Manager Plant Industry Division Nevada Department of Agriculture |
Q: In addition to food safety, the industry must worry about the safety of workers. According to media reports, farm workers at your company were sickened by an agricultural fumigant used on an adjacent field. Can you tell us what happened?
PAM PERI: I’m happy to explain the situation to you. The most unfortunate part is that it’s been blown completely out of proportion. It’s been a feeding frenzy for people in their ignorance. This really was a minor event that was handled poorly by local management authorities. When the emergency response services came out, they jumped to conclusions. They pulled the trigger calling in ambulances and fire engines, and shutting the roads down. God forbid someone’s house was burning down; all the fire fighters were here.
We’ve had every entity here. We had people from San Francisco’s EPA drive all the way here. It was astounding. We spent the whole morning with the Nevada Department of Agriculture. Chuck Moses, Environmental Compliance Section Chief said we could release to the press that a full investigation had been done and there were absolutely no violations or wrong doing. What they found was that we went beyond the call of duty in every respect and if anything our company has been a model in worker safety. We’re debating whether to do another press release because in some ways it just draws more attention to a small incident that was not newsworthy and leaves us vulnerable to another inaccurate, sensationalized story being published.
Q: What in the press coverage was fallacious or exaggerated?
PAM: I’m so frustrated with the media and the erroneous and misleading coverage that I called the editor of the Reno Gazette Journal to give him a piece of my mind and set the record straight. I said what you write has a gigantic impact on the agriculture industry. We’re deeply disturbed and upset about this situation because of the way it was reported. You confuse consumers. There are environmentalists that don’t have an in-depth understanding of the reality of pesticide application. You get ranting maniacs who don’t know the facts and start firing bullets. We already have people throwing around accusations and trying to hurt our reputation and capitalize on the situation for their own gain, which deeply saddens me.
Our food safety and harvest agricultural practices receive superior ratings from reputable third-party audits, and we were one of the first companies in the U.S. to receive clean food standards certification based on criteria set by Scientific Certification Systems. We use a process called NutriClean as part of our food safety and quality program [Editor’s note: you can read about Nutriclean here.] All our products are tested and certified to be entirely 100 percent pesticide-residue free.
We are a very large user of the guest worker program. All these employees were H2A guest workers legally here. We’ve had all kinds of immigration craziness going on, so that’s an important point to make. When the authorities went to speak with the workers, they all had worker protection cards and proof of all training for chemical exposure. This kind of training certification is not typical. We work hard at implementing the best worker safety procedures and Chuck Moses at the Department of Agriculture commended us for that.
Q: Is it true as reported that the implicated chemical was chloropicrin, a tear gas used as a killing agent in past wars?
PAM: The report about the use of the pesticide in World War One certainly was sensationalist. They could have done an entirely different spin. What they did was grab on to the use of this chemical as a wartime killing agent. This chemical has been used for many, many years as a safe fumigant that dispels very quickly and harmlessly into the atmosphere. It’s a common application, used heavily on strawberries.
TIM CUMMINGS: This wouldn’t have even been a blip on the radar, but for a few factors — Pure ignorance about what goes on in the world of agriculture, communication breakdowns, and basic over-reactions. Some poor decisions resulted in a small problem spiraling out of control.
The reality is chloropicrin was used in war in high concentration gas form for adverse effect. The comparison in the media was simply unfair. It is applied in agriculture as an injection in the ground usually 12 to 15 inches as a liquid form to kill different fungus when crops have been rotated. It is always applied late at night and it dissipates quickly in less than 12 hours.
There are laws that it can’t be used if there’s a temperature inversion. In this case, it was applied a day and a half before. The inversion started after it had been applied. There are protections in the law to deal with adverse weather. This incident was a rare occurrence that no one could have predicted.
For the media to make it look like we were gassing our employees is unconscionable. We follow the law to the letter and so does our applicator. More importantly, as it relates to safety of our employees, the company is beyond reproach, taking a leadership role in this area.
Q: In what ways?
TIM: We are one of the largest H2A guest worker program employers. When you have 1,100 people working on your farms over the years, you will have injuries, but if a medical problem ever arises, we pay for the treatment and take care of the workers and have done this for years since the company’s founding. Employees take a safety training class before they go out in the field. They also have ID cards.
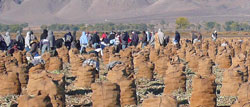
We are dealing with food product and must be extra careful. If you come out to our fields you can see the food safety measures in place. [See photos that accompany this piece]. The first picture above represents some of our employees hand-harvesting in a field. If you look closely, you will find a 500-gallon container of potable drinking water that is in close proximity of our employees at all times. This is an excellent way to make sure that our employees are well hydrated and the water can also be used for emergencies if necessary.
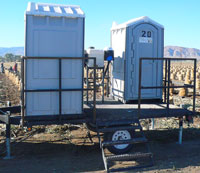
The second picture above is one of our portable washroom facilities. Please notice that there is a soap dispenser, plenty of water for washing and rinsing, paper towels and food sanitizers on every trailer. We have over 100 of these trailer facilities present in the areas where field employees are working and each is maintained and cleaned twice daily. Also please notice that each of these trailers has a full belly plan that is designed specifically to contain anything that may drain from it while on location. These portable washroom trailers are exclusively designed, built and used by Peri & Sons Farms.
Q: How many workers actually became sick from the inversion problem? According to media reports, more than 100 employees were sickened and treated at a medical center.
PAM: The media report was wrong when it said 125 workers were sickened and treated at the medical center. No one was admitted to the hospital. There were some 12 individuals that received an eye wash and had a little bit of respiratory irritation, which completely went away when they got fresh air. They were all back by 1:00 in the field harvesting.
TIM: A triage center was set up outside and workers were told to go home, remove their clothing, take a shower and go back to work. All they needed was fresh air to get it out of their system. The clinic did observe one or two guys for a few hours. For whatever reason, they had other conditions that affected them more strongly. The EPA, OSHA and the Department of Agriculture all came out and said there were no problems here, no rules were broken, no one was injured. It’s aggravating to get negative press when the Department of Ag says we’re a model benchmark as it relates to food safety and employee safety.
Q: Could you give a more detailed account of why you had a problem in the first place? And has anything like this occurred before?
PAM: The problem was a complete fluke due to an unexpected temperature inversion. It’s like controlling lighting. We’ve been in business since 1979 and never had an occurrence like this. This situation was one where Mother Nature affected the way the chemical dissipated. In agriculture, one of the risks is that Mother Nature can play tricks. You can have all the right mechanisms in place and do all the right things.
Q: What are the protocols and regulations?
PAM: The fields where we were using the product were more than a half-mile apart from where product was being harvested. It far exceeded the required distance from the EPA and Department of Agriculture. We use a third-party application company, Silverado Ranch Supply. Russell can tell you more about the process.
RUSSELL WEDLAKE: There are specific regulatory guidelines and detailed application procedures on how deep to go, how far away from residential areas, etc., on the product labels. We’ve been doing this for 11 years and never had problems. I worked with the state department of agriculture, and they said everything we did met or exceeded standards and regulations and the problem was Mother Nature. The state requires a 30-foot buffer between sensitive areas.
If you treat a field within one-quarter mile where people are going to be working, you have to notify the workers and provide water, soap and paper towels in case of accidental exposure. This is standard procedure at Peri & Sons for food safety purposes, so the workers always have these supplies available, even though in this case it wasn’t required. Peri & Sons Farms is one of the leading companies in terms of being proactive in safety and quality.
We actually do the application underground, 12 inches deep, and then it’s covered up with three different pieces of equipment. It slowly changes from liquid to gas and eventually releases out of the soil. It does this at a slow enough rate to mix with the air and dissipate safely. It’s so diluted it’s not even detectable.
We started two days before the inversion, completed application by noon on Tuesday September 25, and the fields we treated were posted to stay out. Workers were taken to the farm at least a half mile away from there to harvest at 7:00 the next morning September 26, and once they had unloaded they started working. Some started noticing itchy eyes and itchy throat and by 7:25, the buses were being loaded and workers removed from the area. There were probably 600 guys out there and 16 to 17 buses.
Some guys were complaining of burning eyes, nose, throat and nausea and were taken to the clinic. We don’t have a hospital here; it’s a medical center. All were looked at and released within a short period of time, but the reports that a hundred or so guys were treated in the clinic is misleading. Almost all were examined outside the clinic in the parking lot; medical staff checked workers’ breathing, their eyes and ears and they were released. Ambulances had been called as a precaution but were never needed.
Q: It’s still not clear to me why the media got it so wrong. Did you communicate with reporters before the articles came out? Why did you wait to issue a press release that clarified all the issues until after the damaging stories went over the wire service?
TIM: The story broke immediately. It’s a local incident so how the heavens did this get to the national media so quickly? And then I find out the guy who runs the emergency response team in our community called media outlets right away. He’s a media hound, and unfortunately he was ignorant of the issues. A television news station decided to use it as its lead report. Adding insult to injury, I had worked there earlier in my career. By the time I called the news media, there were already erroneous reports circulating that people were passing out on the field. No one passed out.
Q: Where did that rumor start?
TIM: We had one worker who was upset and panicked. Somebody from our company hearing the news second-hand called emergency and said people were passing out in the fields. It was a simple breakdown in communication. This has been an agricultural community for 200 years. You’d think emergency teams would know the short-term and long-term effects of these chemicals. For other farms to learn from our experience, be sure emergency teams in your area know what chemicals you use and the remedies.
Q: In a RenoGazette Journal article about the incident, there is a reference to similar incidents that occurred in the Western Nevada region, creating additional sensitivity in this case. I thought this incident was a rarity.
TIM: We saw that and don’t know what they’re talking about. We don’t know of any other incidents. We’re sure there haven’t been any others in our area. I asked Chuck Morris at the Department of Agriculture about this, and he said he didn’t know what this was in reference to and wasn’t familiar with any other incidents. He said that a lot of times these chemicals are being transported in big orange canisters with skull-and-bones warnings and people ask questions.
The Department of Agriculture was fielding phone calls from every news agency asking all kinds of questions that were unrelated to this incident looking for a silver bullet to get a better story. The Reno Gazette attributes the comments about these similar incidents to Ed Foster at the Department of Ag. He might be able to shed more light on this.
ED FOSTER: I was misquoted and tried to rectify that. I had to deal with calls from the EPA on a national level asking about my comments in this article. Here was the crux of it. The bottom line was we were paying close attention to this other exposure in the region this summer. It wasn’t the same fumigant and it had no relation to this incident whatsoever.
It’s difficult with the media here. These smaller media outlets employ one reporter who’s also the dishwasher, bookkeeper and janitor and also trying to get a good story. He’s doing the best job he can in gathering and disseminating information in an entertaining way, and he’s looking for a hook or an angle. Information was coming out fast and furious. I can see how information got misconstrued.
When I think back on this, I got a call from someone at the health department, who we work with on many different issues. She called me to give me a heads up that this kid was doing an article and he was getting information off a scanner (Editor’s note: A radio with access to police, fire and emergency band communications). The fire chief was the instant commander feeding information he was receiving from different sources that was turning out to be wrong.
News came out that there were three unconscious people. There were no unconscious people. It was being reported that 135 people were treated in the hospital for chemical exposure. That was absolute crap. News like that causes pandemonium. Initially eight people were taken from the field and examined. After that, four other people were examined because Peri & Sons was doing the most responsible thing you could do.
I’ve worked my way up in this agency in all different aspects and have dealt extensively with the Peri’s. Speaking as a regulatory officer, they’re a savoir in the Valley. They know what they’re doing. The Peri’s are superstars.
Q: In the end, were you able to clear up misperceptions and get the right information out to the press?
ED: To let people know how news media works, I had an NBC affiliate interview scheduled. The T.V. station was trying to build on this incident and my intention was to control the coverage and get the correct story out. Then a huge immigration story broke and the Peri & Sons incident was put on the backburner. Not one word about it was breathed after the illegal immigrant story took hold. Low and behold, a sweep on illegal immigrants was a more exciting event to cover.
In three weeks, we’ll be issuing a press campaign regarding two programs we have that are very public and very sideways with variables we can’t control involving livestock. We anticipate we’re going to get nailed by the press. We have to get the message out with science and common sense.
Common sense and level heads could have prevented the Peri & Sons incident from turning into complete mayhem.
Q: What other advice can you share with our readers to alleviate such problems in the future?
ED: I’m not an official public relations person, we don’t have funding for this independent function, but I’m in a position to speak with the press. Basically I gave the company line on how I saw this thing unfold. I was getting my information off the Internet, and it was freaky to see the false reports. Cell phone connections aren’t always good in the Valley. We had one inspector that day on site. I wasn’t able to meet directly with people to get first-hand accounts, which would have helped me to better assess the situation. We could have done this better.
PAM: Agriculture companies can avoid this by working more closely with third-party applicators and local emergency teams. If the emergency team had used their head and good judgment and asked what chemical was used, they wouldn’t have had to send all those workers to the hospital when all they needed was fresh air. The emergency response unit created alarm and havoc for no reason.
TIM: At the medical facilities, they didn’t have a translator who could speak Spanish when 50 percent of the community is Spanish-speaking. We need to look at our responsibilities for training emergency response teams and making sure the chain of communication doesn’t break down and then we can curtail the outcome.
Q: In the Associated Press report, it says the company refused questions when contacted by the AP. I’ll read you the exact words: “No comment,” said a man who answered the phone and identified himself only as Nathan. He replied, “not important,” when asked his last name and job title, before hanging up.”
PAM: Part of my frustration with the Reno paper and other reports is that we were contacted for comment but what we said was as soon as we gathered the facts we would issue a press release. We did not want to give out misinformation.
TIM: In one respect, you have to tell employees not to talk to the media. You want one consistent message. We instructed them to direct media questions to me. Nine out of 10 times this would have been sufficient and wouldn’t have led to a problem. We’re farmers; we work. We didn’t know until one-and-a-half hours after that the story went national. In the age of the Internet and advanced technology, news travels fast. We got a call from a friend alerting us that we were breaking a story, but unfortunately in this day and age especially, you can’t count on that.
Our press release was sent out sometime after. I submitted it on September 26 after we had a moment to gather the appropriate information. All information was accurate but at that point very basic. This probably would have been much more effective if it had been released earlier in the day but, of course, hindsight is 20/20, and I have learned my lesson.
We actually had clients on site, a big wholesaler in the Midwest. They left here saying what occurred with the media was a joke. They toured the farm and operations all day long and increased their business with us. They thought the reaction was ridiculous, almost a laughing matter. Anyone who was here couldn’t understand what all the fuss was about. That’s why we try to get people to come out, visit our farm and observe our operations, see how we differentiate from our competition, get the personal touch and feel the passion for what we are doing.
Q: Unfortunately, due to the media coverage of this problem, many consumers haven’t had the benefit your guest customers did of seeing the greater picture in order to put this particular incident in perspective What can be done about that?
TIM: If you sell fresh produce, it’s important to have a crisis plan in place. One lesson was more communication from our management. We needed to provide the right information to avoid such a frenzy. All we had to do was put the workers on buses and get them out for fresh air. We need to take some responsibility for that.
RUSSELL: David (Peri), Pam, the lead guy who does the field work and I have discussed scheduling fumigations around harvesting. If there’s a field on a ranch any time close to harvest, we’ll hold off. We don’t want this to happen. No one does.
TIM: After we harvest, we start preparing the earth for the next harvest season. At that time they do fumigant applications. When we have four or five onion fields close to each other, and three or four are harvested, an application could conceivably be close to a field where we are still harvesting. From now on, the timeframe they’ll wait to apply will be expanded as an additional precaution.
RUSSELL: We’ve done some training with the local fire department and emergency services. We’ve discussed getting together with the authorities, the sheriff, emergency response team, and the fire department to go over the procedures, so they’re educated and no longer unsure of what to do if a problem occurs. And they feel more comfortable around the products we’re using and understand the proper response.
TIM: The produce industry needs to do a better job of protecting ourselves. A lot of farms do excellent food safety and employee safety, but the whole industry needs to invest the money. We have one full time employee overseeing food safety and Pam working constantly on food safety and employee safety. The company commits huge financial investments. In the end, responsibility comes down to the produce buyers. They need to require strong and specific food safety programs from their vendors — truly audited by third parties they can trust.
You have to feel sorry for the Peri family. What a mess. Yet the lessons for the broader industry are also clear. There is little point in blaming the media. You can pretty much expect the consumer media to zoom in on the most provocative part of the story. The fact that the gas had been used in war as an instrument of chemical warfare was certainly attention-getting.
Hysteria and overstatement fill a vacuum, and so everyone has to be prepared to communicate the truth, promptly and in context. Also the interview reveals some excellent specific points, such as the need to educate emergency workers on each chemical and how to deal with exposure as well as the importance of having emergency staff that can speak the language of the workers.By the way, if we ever succeed in getting the pathogen issue behind us, we can expect a shift in attention toward pesticide usage and, especially, the effect of pesticides on farm workers.
Many thanks to Pam, Tim, Russell and Ed for sharing their story with the industry and thus giving us all a lesson on the importance of emergency planning and reminding us that we cannot expect that others — rescue workers, the media, etc., — will have an understanding of agriculture unless we make it our job to educate them.